Compa
ny InsightSafe berthing of vessels – reliable and durable fenders make it work
What exactly makes a good fender? The first White Paper of ShibataFenderTeam “Compounding – A winding road” is taking a closer look at the raw materials used in rubber production, the physical properties of a fender, and their correlation with the compound’s composition.
SPC Cone Fender System | Ferry Terminal | Sweden
Safety, reliability, durability – the performance requirements of a marine fender boil down to these three aspects, and rightly so. Fenders are meant to create a safe environment for ships and passengers while protecting port infrastructures and all personnel working there – reliably during the design life and beyond. This is the ideal that ports and port operators strive for.
When considering the product features required for such high performance, waters tend to become somewhat murky. There are international standards and guidelines providing guidance as to the physical properties of rubber fenders – like PIANC2002 and ASTM D2000. However, there is no international standard specifying the chemical composition of the rubber compound used in the manufacturing of rubber fenders.
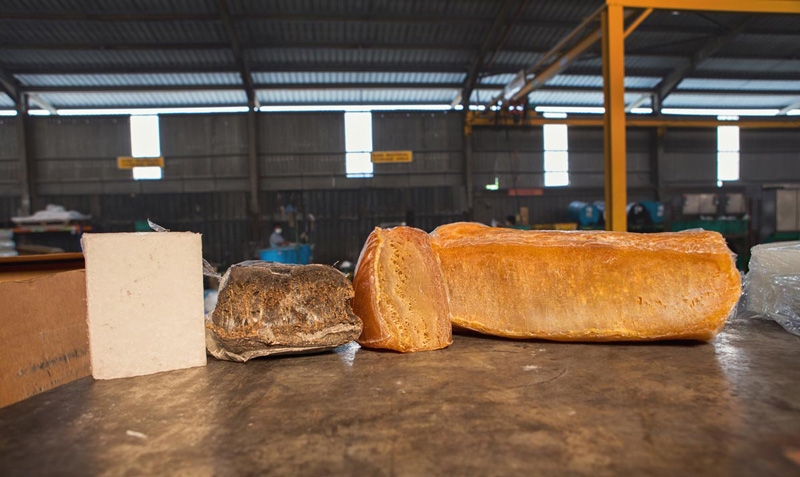
CSS Cell Fender System | Bulk & Aggregate Jetty | Oman
Industry standards are delineating a clear goal in the manufacturing of marine fenders, their performance, physical properties and durability, but there is no recommendation as to how to get there. The reason for this is simple: no two fender projects and no two fender manufacturers are alike. Each project has unique requirements that necessitate customized rubber compositions.
All of this provides a lot of room for market differentiation and opportunities for fender manufacturers to present their own best practice-approaches to producing high performance products. Yet, it has also become the breeding ground for some widely accepted – and by some stakeholders actively advocated – misconceptions about compound production, the most prevalent one asserting that the quality of a fender is primarily determined by the chemical composition of its rubber compound.
“At the ShibataFenderTeam Group (SFT), we believe that the quality of a fender should be measured by its performance, i.e. by the degree to which a fender lives up to the requirements of its specific field of application,” says Mr. Dominique Polte, Board Member ShibataFenderTeam.
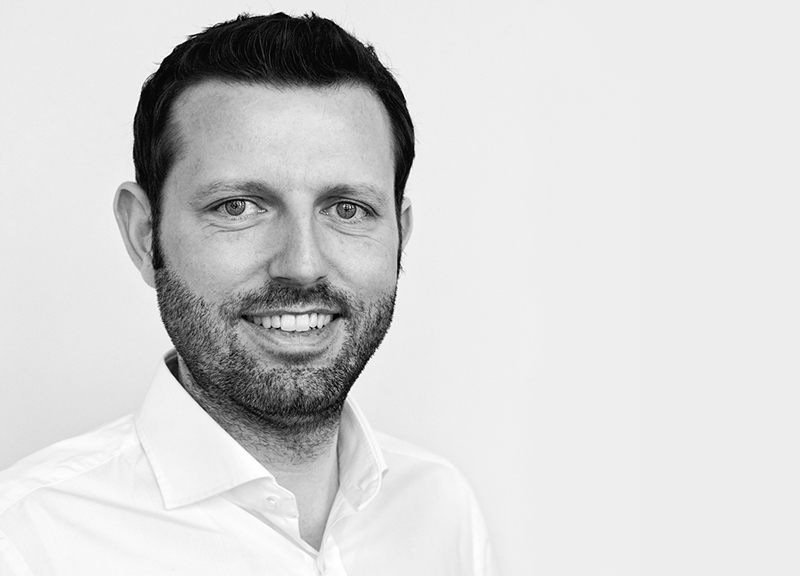
FE Element Fender System | Ferry & RoRo Terminal | Germany
As a reinforced rubber compound is the core of any fender, the first part of the SFT White Paper Series on fender manufacturing “Compounding – A Winding Road” focuses on the raw materials used in rubber production, the physical properties of a fender, and their correlation with the compound’s composition. Its goal is to detail the considerations relevant to determining what makes a good fender.
It finds that in fender manufacturing, physical properties are the only reliable indicator of the quality of a rubber compound that is defined by international standards. In addition, the white paper recommends that ratios of fillers and reinforcement agents such as carbon black (CB), calcium carbonate (CC) and silica should be determined by specialists with profound material knowledge, as amount and particle size greatly influence the compound as well as its performance and durability. Furthermore, the paper draws attention to the fact that rubber compounds mixed correctly with CC by experienced manufacturers comply with and surpass international testing standards.
The four-part White Paper Series aims to provide an unbiased view of what exactly makes a good fender – from source materials to manufacturing process.
Part I approached this question by taking a closer look at the constituent components of a fender and their role in determining performance-relevant physical properties. Parts II and III detail the mixing and curing process involved in producing a high-quality rubber fender. Part IV concludes the series with a detailed report about testing.
Get your complimentary version here.
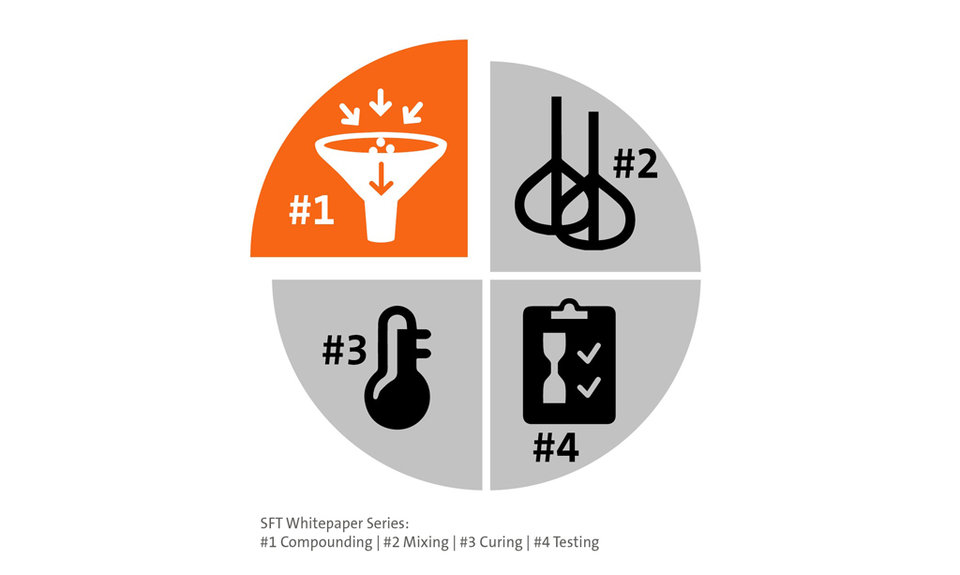
Engineering to ensure a safe environment for ports and the shipping industry
POOR PLANNING AND OVERCONFIDENCE: THE MAIB’S MAIN FINDINGS
If there is one takeaway point from the inquiry it is that poor planning was at play.
Investigators discovered the lead pilot had not informed the bridge team of his plan for the turn around Bramble Bank. There was an “absence of a shared understanding of the pilot’s intentions for passing other vessels or for making the critical turns during the passage”.
Elsewhere, the master and port pilots were blamed for “complacency and a degree of over-confidence”.
There was an “absence of a shared understanding of the pilot’s intentions”
CMA CGM, which took delivery of the Vasco de Gama in July 2015, has acknowledged MAIB’s findings, and claims to be addressing the aforementioned issues raised in the report.
“Following this grounding, CMA CGM and ABP [Associated British Ports] Southampton have been working together,” said a spokesperson for the company in an email.
“As mentioned in the MAIB official report, CMA CGM has already taken measures to prevent this type of incident to happen again. CMA CGM is strongly committed to ensuring the safety of its operations and its crews in accordance with local and international regulations.”
All straight-bat stuff. ABP could not be reached for comment.
Unavoidable inquiry: why the MAIB inquiry needed to happen
Simon Boxall, a maritime expert from the University of Southampton, believes MAIB’s findings to be fair, despite Bramble Bank’s reputation as “a navigation hazard” due to it susceptibility to “slight movement after major storms”.
“Looking through the report there was no evidence of unforeseen mechanical failure on the ship, nor of abnormal weather conditions,” he says.
“On that basis, the two pilots and the ship’s master should have been in a position to safely navigate the vessel into port. It would appear to be user error – which is what the report says in so many words.
Introducing ways of reducing user error can only be seen as a good move
“In light of this, introducing ways of reducing user error can only be seen as a good move.”
Boxall also acknowledges things could have been a lot worse. As the Vasco de Gama was re-floated relatively quickly, the port didn’t suffer any kind of blockage – which, given the vessel’s size, would have brought Southampton to “a standstill”.
Neither did the vessel endure any serious damage. Nonetheless, an investigation was still necessary.
“If reports such as this are not produced then the safe navigation of shipping is not improved,” says Boxall.
“In the same way an airline near-miss is thoroughly investigated, it is important that the same is done for shipping – not as a witch hunt, but as a fact finding investigation to improve safety.”
Svein Kleven is senior vice president of engineering and technology for Rolls-Royce. Image courtesy of Rolls-Royce