Company Insight
Sponsored by NAPA
To solve shipping's toughest efficiency challenges, we need to make use of digital twins
Huge efficiency savings from voyage optimization are there for the taking – if we combine ship design models with operational data, says Pekka Pakkanen, NAPA, Director, Sales, NAPA Shipping Solutions.
Caption
The pressure owners and operators are facing in relation to optimizing vessel performance has never been greater. They already face a clear target from the IMO to reduce carbon emissions by 50% by 2050, compared to 2008 levels, and many other influential bodies – such as the EU and Hapag-Lloyd – have argued that this timeline should be accelerated.
Owners and other shipping stakeholders are therefore tasked with solving this challenge, however, have not been provided with clear guidance or meaningful assistance on how best to achieve such carbon reductions. Not only are they required to deal with economic recovery in light of the global pandemic, but they must also evaluate a range of future fuels and technologies, none of which are yet mature, while managing their bottom line.
So, where do we look for the answers? The answer comes when we start to combine ship design expertise with powerful analytical tools.
From naval architectural models to digital twins
For over 30 years NAPA has been a trusted design platform for the initial and basic design of any ship type or marine vessel. NAPA is the standard software for ship 3D design and analysis used daily by over 2500 naval architects, engineers and steel structure designers, to ensure the ships which are built are safe, comply with regulations, and are most efficient for the purpose they are built. The name NAPA originally comes from the words Naval Architectural Package, and true to the name, NAPA covers a wide range of calculations and analyses related to, for example, hydrostatics, intact and damage stability, longitudinal strength, weight, and hydrodynamics.
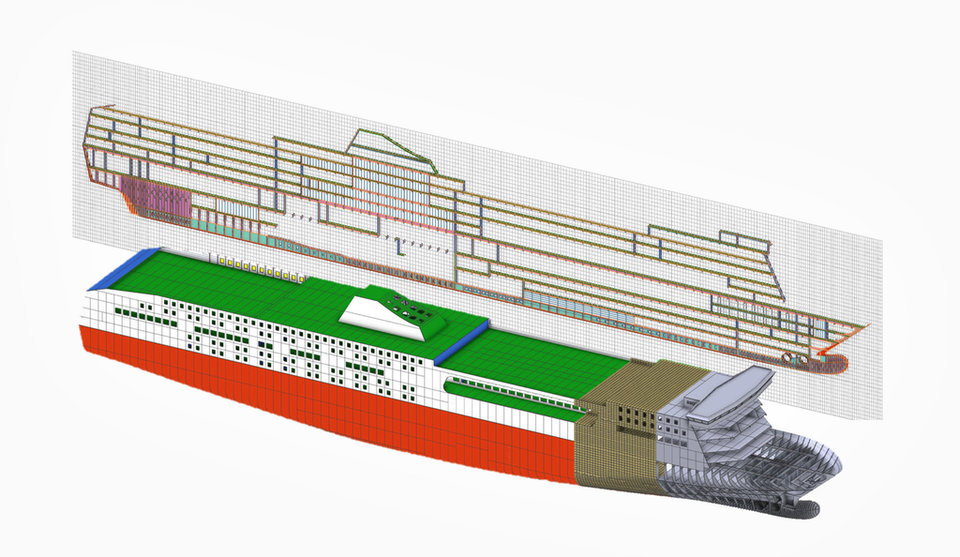
Most ships in the current world fleet have been designed with NAPA’s design platform.
After the ship is built and sailing, the NAPA model creates the core of a digital twin for the physical ship, when combined with data about how the ship is being operated, and what environmental conditions it is encountering. This digital twin then offers endless possibilities for different ship operation stakeholders to monitor, plan, analyze and optimize safety, stability and performance for any vessel or fleet.
One example of utilizing the design-phase ship model later in ship operation is NAPA Loading Computer. It is used to plan and optimize load, while ensuring all regulatory safety and stability criteria are met. Another example is NAPA Emergency Computer, which guides crew to sail with maximum safety by continuously monitoring the vulnerability of the ship. If flooding would occur, advanced flooding simulation provides decision support for the crew in the highly stressful situation. Thus, the same analyses and calculations that are used to engineer and iterate the ship design before building, are utilized to play with scenarios to find how best to operate the vessel to run as safely and efficiently as possible.
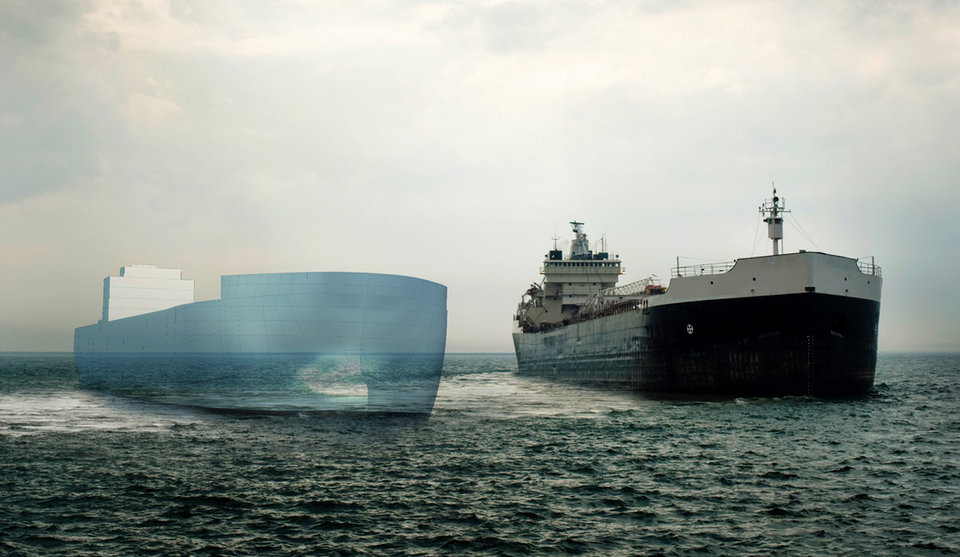
NAPA Fleet Intelligence combines design models with operational data for maximum efficiency savings.
Bringing it all together – combining design models with performance data
By combining hydrodynamic modelling with engine data, weather data, operational data, and optimization technology; NAPA Fleet Intelligence and NAPA Voyage Optimization can optimize routes and operations, and realistically model fuel consumption. We have built hydrodynamics-based NAPA Performance Models of the entire global fleet’s ~55 000 vessels according to their publicly available main characteristics and dimensions. This enables improved estimates of required voyage time and sea margin, planning of hull maintenance and provides up-to-date information on the ship performance for fuel efficient voyage optimization.
We simulate ship resistance in actual weather conditions, such as wind, waves and shallow water, and combine the data with the actual location of the vessel and the actual speed and heading of the vessel. Using this model, it is possible to more accurately monitor and optimize performance and, for example, examine factors such as the effects of hull fouling.
This creates a virtuous circle: the more we apply our data, analysis and expertise, the better the models become and the more we are able to make shipping energy-efficient. It is no longer idealistic to believe that we can deliver more goods with less emissions.